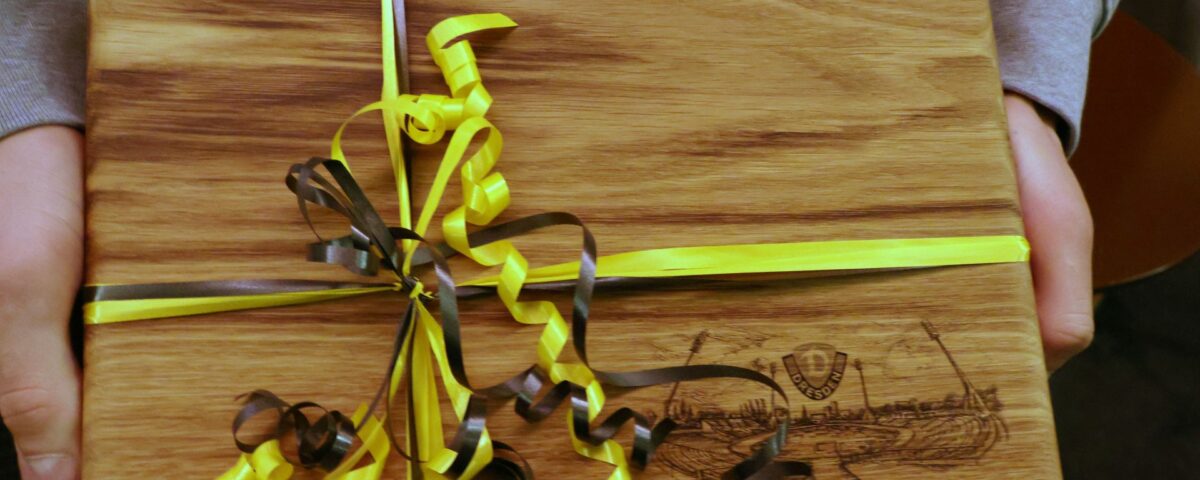
Ein ganz besonderes Highlight fand für mich Ende 2023 statt, als ein Schneidebrett Dynamo Dresden aus Eiche für eine Veranstaltung am 5. Dezember 2023 hergestellt werden sollte. Frühere Spieler und weitere Personen sollten als Dankeschön die Schneidebretter und einen Dresdner Christstollen erhalten.
Letztlich sind es insgesamt zwei Chargen geworden, einmal mit Eicheholz von Bauhaus, das zweite Mal mit Holz von einem Holzhändler in Pulsnitz. Hier erfährst du, was die einzelnen Schritte sind bei den beiden Chargen, denn bei der "Pulsnitz-Charge" waren noch einige Schritte mehr notwendig.
Lest in diesem Beitrag, wie das Holz von der Bohle bis zur Übergabe verarbeitet wird.
Planung
Die Planung war einfach und ich brauchte keine SketchUp-Zeichnung, denn die ungefähre Breite und Länge war das Maß einer Stollenverpackung. Wie bei allen Brettern, die ich herstelle, wurde auch hier eine 45-Grad-Gehrung unten angebracht, die als Griffkante dient, damit man die schon recht schweren Bretter gut von einer planen Oberfläche hochheben kann.
Oben fräse ich immer eine kleine Rundung an, dafür hatte ich mir vor einigen Jahren das 22-teilige Fräserset von ENT (hier bei Amazon kaufen *) gekauft. In diesem Set hat man viele Fräser schön beieinander und kann sich immer den passenden Fräser heraussuchen.
Materialkauf
Für die erste Charge habe ich drei Eichebohlen bei Bauhaus besorgt, da es gleich hier quasi um die Ecke ist und die Herstellung recht schnell gehen musste. Als Info: Für jede Bohle mit einem Endmaß von 1,20 m Länge, 36 bis 40 cm Breite und einer Stärke von 26 mm habe ich 37,80 Euro pro Stück bezahlt, was einem Meterpreis von 31,50 Euro entspricht. Sind also astronomische Preise, aber wie gerade schon erwähnt, musste es schnell gehen. Der Vorteil dieser Bohlen war, dass ich sie nicht noch extra hobeln musste. Allerdings hatten sie einige tiefere Löcher, Astlöcher und andere Macken, aber für mich stellen diese Macken keinen Makel dar, denn diese sind ja ein Merkmal von Holz und Natur. Aus einer Bohle habe ich also ca. drei Bretter herausgesägt, der Rest war Abfall. Schon allein für das Material also pro Brett ca. 12,60 Euro - wohlgemerkt ohne Arbeitszeit, Abnutzung der Maschinen, Stromkosten oder Gravurzeit.
Die zweite Charge Holz habe ich bei einem kleinen Holzhändler in Pulsnitz gekauft. Die Bohlen waren ein wenig länger, ca. 1,40 m, die Breite variierte zwischen ca. 22 cm und ca. 25 cm, die Stärke betrug ca. 25 mm. Es ist jedoch anzumerken, dass dies nicht die Endstärke ist, denn die Bretter musste ich noch hobeln, weil sie ein wenig verzogen waren. Bei dieser Charge haben die Bohlen jeweils 9 Euro gekostet, aber insgesamt musste eben auch mehr Arbeit hineingesteckt werden. Zudem hatte eine oder zwei Bohlen einige Wurmgänge, die ich so weit wie möglich weggesägt bzw. weggeschliffen habe.
Es gibt also bei beiden Chargen jeweils Vor- und Nachteile, ich habe bisher aber noch nicht herausgefunden, welches nun besser für meine Bedürfnisse ist.
Bei beiden Chargen habe ich mich im ersten Schritt aber um die Rinde bzw. Waldkante gekümmert.
Waldkante absägen und auf Länge sägen
Im ersten Schritt muss die Rinde entfernt werden, denn die Bretter sollen eine schön glatte Kante haben. Hier kam mal wieder meine geliebte Festool TS55 (bei Amazon kaufen *) zum Einsatz. Vor einigen Jahren habe ich sie mir genau für solche Fälle zugelegt - große Platten für die Tischkreissäge vorbereiten oder Baumkante bzw. Rinde absägen.
Die beiden Klappböcke (bei Amazon kaufen *) kamen ebenso wieder zum Einsatz. Also jeweils eine Bohle auf die beiden Klappböcke bugsiert, mit den Festool-Zwingen (bei Amazon kaufen *) befestigt und die Festool-Führungsschienen FS 1400/2 (bei Amazon kaufen *) hervorgezaubert.
Diese haben eine Länge von 1,40 m - daher auch der Name FS 1400 - und hatten damit für die Bauhaus-Bohlen glücklicherweise die passende Länge, ohne zwei Führungsschienen zusammenzusetzen. Da die Pulsnitz-Bohlen zu lang waren, um von Anfang bis Ende einen glatten und durchgehenden Schnitt herbeizuführen, musste ich für diese Bohlen eben doch meine beiden Festool-Führungsschienen zusammenstecken.
Da dieser Schritt dazu gedacht ist, eine gerade Kante als Referenz zu haben, an der man sich immer wieder orientieren kann, war es wichtig, dass genau gearbeitet wird. Die Bauhaus-Bohlen hatten am Ende eine Breite von ca. 33 cm, die aus Pulsnitz hatten unterschiedliche Breiten, von ca. 20 cm bis zu 24 cm. Für die bei diesem Projekt hergestellten Bretter war eine Breite von mindestens ca. 21 cm notwendig, sodass einige Abschnitte nicht geeignet waren. Die kommen dann für spätere Projekte zum Einsatz.
Und der beste Tipp, den man für diese Art des Sägens noch geben kann: Immer schön aufpassen, dass du mit der Tauchsäge Festool TS55 nicht das sägst, was nicht gesägt werden darf. Nicht dass beim Sägen die Sägeböcke im Weg sind und es plötzlich funkt. ;-) Also lieber einmal mehr prüfen, ob die Säge neben den Sägeböcken entlanggeführt wird oder nicht doch mitten durchs Metall sägt.
Wenn die eine Seite der Waldkante nicht mehr vorhanden ist, ist für mich der beste Zeitpunkt, die Bretter gleich auf Länge zu sägen. Die Länge ist eigentlich die Breite, da die Bretter mit der Maserung von links nach rechts hingelegt werden sollen. Beim Zersägen auf die ca. 30 cm ist extrem wichtig, konzentriert zu arbeiten, vor allem bei den Brettern, die noch nicht abgerichtet und plangehobelt wurden. Wenn man nicht aufpasst, kann sich das Holz verkanten und im schlimmsten Fall wegfliegen, das will ich natürlich verhindern. Um dies zu verhindern, ist der Spaltkeil da, der bei mir IMMER dran bleibt.
Wenn ich die Bretter auf die passende Länge säge, achte ich gleich darauf, dass Risse so weit wie es geht weggesägt werden. Oft habe ich deswegen auch mehr als 30 cm abgesägt, denn du kennst ja den Spruch: Abgesägt ist schnell, drangeklebt nicht so schnell. ;-)
Abrichten und Hobeln
Dieser Schritt war am aufwendigsten, musste aber nur bei den Eichebohlen aus Pulsnitz durchgeführt werden, da die Bauhaus-Bohlen schon geschliffen im Regal standen.
Bevor ich zum eigentlichen Schritt des Abrichtens kommen kann, muss ich prüfen, ob die Breite der Bohlen passt oder ich noch ein wenig mehr absägen muss. Mein Abricht- und Dickenhobel Metabo HC260C hat eine maximale Abrichtbreite von 260 mm. Das sind 26 cm. ;-) Übrigens war damals Metabo noch blau, nicht grün wie heute, ganz früher ist der Firmenname Elektra Beckum gewesen, den vielleicht einige von euch kennen. Noch ein witziger Fun Fact zu dem Hobel: Mein Mitmieter in der Werkstatt hat ebenfalls einen Hobel: Elektra Beckum HC260C. Also ja, wir haben den gleichen Abricht- und Dickenhobel, nur dass seiner älter ist als meiner.
Wenn das passt, kann es nun endlich losgehen. Hauptsächlich für diesen Schritt habe ich mir mit dem 3-D-Drucker einen Push Block gedruckt, anhand dessen Farbe sofort ersichtlich ist, dass es meiner ist. ;-) Ein Foto des barbie-farbenen Push Blocks findest du ein Stück weiter unten. Ich habe mit Sekundenkleber noch eine Antirutschmatte unten angeklebt.
Beim Abrichten und auch beim Dickenhobeln muss unbedingt auf die Sicherheit geachtet werden, denn die Hobelmesser sind extrem scharf! Und immer konzentriert bei der Sache sein!
Eine Referenzkante habe ich ja nun schon: die abgesägte Baumkante. Zunächst sollte man den Anschlag auf der rechten Seite so einstellen, dass ein rechter Winkel vorhanden ist, sonst wird am Ende alles schief. Danach schaust du dir das Holz an, ich habe die Seite genommen, an der die Außenkanten nach unten gewölbt waren.
Wenn das erledigt ist, kommt der Umbau der Abrichte zum Dickenhobel. Das dauert immer einige Minuten, doch wenn der Umbau erfolgt ist, wird die Öffnung auf die stärkste Platte angepasst. Ich schiebe die Platten immer mehrmals auf der vorher ungehobelten Seite durch, an der Oberfläche erkennt man sofort, wann alles schön abgehobelt ist. Sobald diese Seite auch schön plan ist, schiebe ich die andere Seite auch immer nochmal durch den Hobel. Leider ist es bei meinem Metabo-Abricht- und -Dickenhobel so, dass offenbar eine Walze seine Spuren auf dem Holz hinterlässt.
Nach ungefähr sechs Stunden war der ganze Schritt des Hobelns dann erledigt und ich war echt froh, als alles geschafft war!
Griffkante sägen
Nach dem extrem aufwendigen Schritt des Hobelns folgt nun ein recht schneller Schritt, das Sägen der Griffkante rundherum. Diese Art der Griffkante wird auch "Schweizer Kante" bezeichnet und ich nutze diese immer, weil die Bretter relativ schwer sind und mit dieser Verarbeitungsweise besser von einer planen Arbeitsplatte hochgehoben werden können.
Nachdem ich bei den Pulsnitz-Brettern die zweite Baumkante abgesägt habe, erfolgte die Sortierung nach der kurzen Seite, damit der Schritt nicht mehr so lang dauert. Den Parallelanschlag habe ich auf einen cm schmaler eingestellt als das Brett ist, und dann das Sägeblatt auf 45 Grad gedreht. So habe ich die beiden langen Seiten mit der Griffkante versehen, danach wurden die Bretter nach der langen Seite sortiert. Auch hier habe ich jeweils den Gehrungsschnitt einen cm hineinversetzt und dann waren alle Bretter mit einer hübschen Schweizer Kante versehen.
Nun kann es zur Oberseite gehen, die mit einer tollen Rundung versehen wird.
Rundung anfräsen
Nun komme ich also zum Fräsen der Oberseite. Das ist der Schritt, der am schnellsten geht, da ich einfach zweimal rundherum die Tischoberfräse ansetze und nichts an den Einstellungen verändern brauche. Je nachdem, wie viel Material weggenommen werden soll bzw. wie rund die Fräsung sein soll, muss der Fräser mit dem Kugellager unten nach oben oder unten versetzt werden. Normalerweise wird die Oberfräse mit der Hand geführt, daher ist das Kugellager, was man an das Werkstück anlegt, unten. Da ich aber eine Tischfräse habe, sieht es genau andersherum aus. Ein wenig verwirrend, aber eigentlich ganz einfach.
Ich habe die Höhe, in der der Fräser aus dem Tisch herausschaut, so eingestellt, dass sich keine neue Kante bildet, was vorkommen kann, wenn zu viel Material weggenommen wird und der Fräser zu tief ins Material eindringt. Bei anderen Brettern habe ich das mit Absicht gemacht, weil es mal anders aussieht und nicht so langweilig ist. Letztlich muss man selbst wissen, wie es besser gefällt oder was gewünscht ist.
Das Einzige, worauf ich achten musste, ist die Fräsrichtung. Damit man nicht durcheinanderkommt, ist auf den Fräsplatten ein Pfeil abgebildet, der die Richtung zeigt, in der das Werkstück in den Fräser geschoben werden soll. Das bedeutet, dass im Gegenlauf gefräst wird. Wenn im Gleichlauf gefräst werden würde, könnte das Werkstück mit dem Fräser mitgerissen werden. Damit habe ich leider auch schon Erfahrung machen müssen, weshalb ich immer darauf achte, dass wirklich im Gegenlauf, also entgegen der Drehrichtung des Fräsers, gefräst wird.
Schleifen
Der letzte Schritt in der Werkstatt ist für mich der Schleifvorgang. Ich beginne mit einer 80er-Körnung, das heißt es wird zunächst sehr grob abgeschliffen. Dafür nutze ich den Exzenterschleifer Mirka Deros 650CV (hier bei Amazon kaufen *), den ich schon einige Jahre besitze. Leider funktioniert gerade meine Absaugung nicht gut, weswegen ich eine FFP2-Maske aufsetzen musste, denn Eichestaub ist nicht wirklich gesund und kann unter Umständen zu Krebs führen, was natürlich niemand will.
Es wurde immer alles geschliffen, das heißt die Oberseite, die Unterseite, die Griffkante und die Rundung. Nach der groben 80er-Körnung ging es weiter mit Korn 120, 230 und 320. Ich schätze, dass für alle Bretter ca. 1,5 h benötigt wurden. Danach haben sie sich aber schön glatt angefühlt. Die Spoilerwarnung kommt schon mal jetzt: Das wird sich beim Kontakt mit Wasser ändern, denn beim Schleifen werden die Fasern nach unten gedrückt, beim Kontakt mit Wasser stellen sie sich wieder auf.
Beim Schleifen muss darauf geachtet werden, dass nicht zu stark gedrückt wird, da sonst die Schleifspuren sichtbar werden können. Immer schön gleichmäßig über das Holz gehen und die eventuell vorhandenen Spuren vom Hobeln entfernen. So wird das Holz schön aussehen.
Habt ihr den Mirka-Schleifer auch? Ist es bei euch auch so, dass das Kabel aus der Befestigung herausrutscht? Ich werde demnächst Mirka anschreiben, was ich dagegen machen kann, denn dieser Fehler nervt mich echt extrem, da ich nicht so sehr drauf achte und plötzlich geht die Maschine mitten im Schleifvorgang aus.
Gravur
Die Bretter für den Fußballverein Dynamo Dresden habe ich nach dem Schleifen mit nach Hause genommen, da der Diodenlaser Ortur Laser Master 3 mit dem älteren 10-Watt-Modul (hier bei Amazon kaufen *) dort steht. In der Werkstatt habe ich den großen CO2-Laser von Omtech mit 80 Watt (hier bei Amazon kaufen *) stehen, aber ich wollte eine sehr feine Gravur und die kann ich zurzeit am besten mit dem Diodenlaser herstellen. Das dauert zwar länger, aber das Ergebnis sieht aus meiner Sicht viel schöner aus.
Das Bild, was graviert werden soll, zeigt eine Skizze des alten Rudolf-Harbig-Stadions, was unser Fußballstadion in Dresden ist. Mittlerweile wurde das Stadion neugebaut (2009), die Fans sind aber immer noch so erstaunlich wie eh und je. Wer sich ein wenig zur Geschichte des Stadions informieren möchte, kann das hier tun.
Bei Eiche-Massivholz benötige ich schon recht viel Leistung bei relativ geringer Geschwindigkeit. Ich habe für die Gravur eine Geschwindigkeit von 1700 mm/min bei einer Leistung von 85 Prozent genutzt. Als Bildmodus entschied ich mich für Stucki bei einer Auflösung von 254 DPI. Für eine Gravur in einer Breite von 13 cm hat der OLM 3 ca. 45 Minuten benötigt. Das Ergebnis siehst du in den folgenden Bildern.
Da ursprünglich geplant war, alte Fotos von verschiedenen Spielern zu nutzen und diese auf die Bretter zu bringen, habe ich eine Gravur mit einem bearbeiteten Bild von Hartmut Schade auf einem Reststück Eiche probiert. Sieht genial aus, oder? Diese Gravur hat aber ganze vier Stunden (!) gebraucht, weil sie über die gesamte Breite und Länge des Reststückes ging.
Endbehandlung
Bei der Endbehandlung habe ich bei den Bauhaus-Brettern auf das Schneidebrettöl (hier bei Amazon kaufen *) sowie das Schneidebrettwachs (hier bei Amazon kaufen *) von Clark's gesetzt, da es lebensmittelecht ist und sich gut verarbeiten lässt. Außerdem riecht es richtig gut nach Orange und Zitrone. Beide zusammen gibt es übrigens auch als Set (hier bei Amazon kaufen *), was ich mir vor einigen Jahren selbst gekauft habe.
Bei den Pulsnitz-Brettern habe ich teilweise auch das obige Öl und Wachs genutzt, manchmal aber auch das Hartwachsöl von Linea Natura und zusätzlich das Schneidebrettwachs von Clark's.
Durch die Endbehandlung wird zum einen die Maserung angefeuert, zum anderen eine das Holz schützende Schicht aufgetragen, wobei beim Ölen darauf zu achten ist, dass man es nach einiger Zeit wieder abnimmt, sonst kann es hässliche Flecken geben oder alles kleben. Ich bringe es mit einem Werkstatttuch (hier bei Amazon kaufen *) auf und nehme das überschüssige Öl mit einem weiteren ab. Nach der Benutzung unbedingt darauf achten, dass die ölgetränkten Tücher an der Luft oder ausgebreitet aushärten, denn es kann im schlimmsten Fall zu einer Selbstentzündung kommen!
Das Cutting Board Wax bringe ich meistens mit der Hand auf, weil ich so gleich merke, wenn noch ein Rest vorhanden ist, der noch nicht verteilt wurde. Das kann man aber auch mit einem speziellen Applikator für Wachs (hier bei Amazon kaufen *) erledigen.
Abschluss
Am Freitag, den 1. Dezember 2023, war es dann so weit und ich habe die Bretter im Dynamo-Fanshop selbst ausgeliefert, zu dem Zeitpunkt noch umwickelt mit blauen Werkstatttüchern, da die Endbehandlung erst einen Tag zuvor stattgefunden hat. Ohne die Werkstatttücher hätten das Öl und Wachs überall Spuren hinterlassen, was ich natürlich verhindern wollte. Bei der Abgabe habe ich gleich die Möglichkeit genutzt, mich mal im Fanshop umzuschauen und mit einer Mitarbeiterin ins Gespräch zu kommen, was richtig schön war.
Die Veranstaltung hat am 5. Dezember 2023 stattgefunden und wie mir im Nachgang berichtet wurde, sind die Bretter sehr gut angekommen. Ob sie jetzt als richtige Schneidebretter genutzt werden oder als Deko dienen, weiß ich zwar nicht, aber durch diesen Blogbeitrag soll nochmal gezeigt werden, dass in den Brettern sehr viel Arbeit steckt.
Wenn die neuen Besitzer Fragen haben oder ich das Brett nochmal schleifen oder hobeln soll, können sie sich gern an mich wenden. Die Kontaktdaten sind im Impressum zu finden.