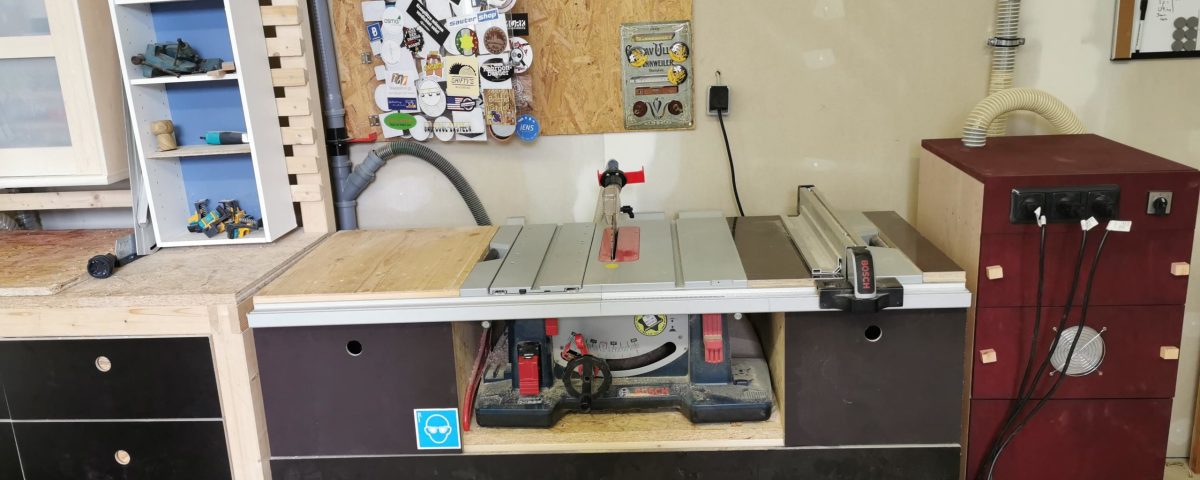
Nachdem ich seit 2018 meine eigene Werkstatt hatte, wollte ich mich nun endlich an die Absauganlage machen. Eigentlich war das schon für die alte Werkstatt gedacht, aber ihr kennt das ja, da kommt immer etwas dazwischen und schwubbs, ist ein Jahr 'rum.
Planung
Dieses Mal habe ich nicht selber geplant, sondern mir von Michael Truppe (www.heimwerker-helden.de) die Pläne geholt inkl. den dazugehörigen Videos. Da ich so etwas noch nie gebaut hatte und ich Verschnitt total hasse, war das für mich die bessere Variante.
Die Pläne an sich sind aber verbesserungswürdig, denn zum Beispiel steht nirgendwo dabei, bei welchen Maßen es auf die eigene Turbine ankommt. Ohne das Video gesehen zu haben kann man hier schnell in die erste Falle stolpern. In den Plänen gibt es Links zu den Videos (auch inkl. der Einschaltautomatik, die ich aber nicht nutze, siehe unten). Die Videos habe ich mir erstmal runtergeladen, weil ich in der Werkstatt kein Internet habe und jedes Mal Datenvolumen zu verbraten wäre dann doch etwas unverhältnismäßig gewesen.
Materialkauf
Der Materialkauf ging schon weit vor dem eigentlichen Bau los. Ich hatte wirklich nichts da außer einem bei eBay Kleinanzeigen kostenlos ergatterten Staubsauger, den ich schon von vornherein für diese Absauganlage nutzen wollte.
Neben - natürlich - dem ganzen Holz braucht man unter anderem folgende Dinge:
- Dichtungsbänder für die unteren drei Fächer (ich habe diese hier * genommen)
- HT-Rohre DN 50
- 1x Länge 250 mm (für den Ausgang nach oben; hier * kaufen)
- 4x Bogen 45 Grad (zwei für den Eingang, zwei für die Verbindung mit dem 87er-Bogen; hier * kaufen)
- 1x Bogen 87 Grad (über dem Staubsaugerbeutel, hier * kaufen)
- HT-Muffe (zwischen dem 87er-Bogen und dem ersten 45-Grad-Bogen; hier * kaufen)
- 1 Rohr z. B. 500 mm, von dem man mindestens zwei Stücke abschneiden kann (für die Verbindung der HT-Muffe mit dem 87-Grad-Bogen und dem Dust Commander mit dem 45-Grad-Bogen; hier * kaufen)
- Anschaltautomatik (z. B. Eltako, hier *)
- 4 Rollen (z. B. hier * kaufen)
- Nockenschalter (hier * kannst du meinen kaufen, man kann aber natürlich auch einen einfach Schalter nehmen)
- Steckdosen (ich habe die hier * genommen und der passende Abdeckrahmen hier *)
- Dust Commander oder Alternativen (das Original kannst du hier * kaufen)
- längere Maschinenschrauben M 6 zur Befestigung des Dust Commanders, ca. 50 mm lang, da die Originalschrauben zu kurz sind (hier * kaufen)
- Unterlegscheiben DIN 9021 M 6 (hier * kaufen)
- Karosseriescheiben M 6 (hier * kaufen)
- Gewindestange M 6 in 1 m Länge (hier * kaufen)
- Winkelschleifer für das Teilen der Gewindestange in 5 cm lange Stücke (meiner ist der hier *)
- Sechskantmuttern DIN 934 M 6 (hier * kaufen)
- ggf. Noppenschaumstoff zur Geräuschreduzierung der Turbine (hier * kaufen),
- ggf. ein leeres Reihenklemmengehäuse für die Verkabelung (hier * kaufen)
- 2 Lüftergitter (hier * kaufen)
- Vlies oder Stoff für die Abdeckung des von vorn sichtbaren Lüftergitters (wenn ihr noch Lüfterfilter vom Badlüfter da habt, geht auch das, aber ihr könnt das auch hier * kaufen)
- Gewindeschneider M 6 für die Drehknaufe vorne (ich habe mir die hier * gekauft)
- einen Dremel oder etwas, womit man kleine Nuten einlassen kann für die Mechanik der Drehgriffe (ich habe den DREMEL® MULTI-MAX MM40 (MM40-1/9), aber besser wäre ein aktuelles Modell, z. B. den hier * kaufen)
- Tellerschleifer, um die Karosseriescheiben abzuschleifen (z. B. hier * kaufen)
- Cuttermesser (hier * kaufen) zum Schneiden des Dichtungsbandes und des Noppenschaumstoffs
- Winkel (meinen kannst du hier * kaufen)
- Akkuschrauber (meinen kannst du hier * kaufen)
- Kreisschneider (z. B. hier * kaufen) bzw. zusätzlich Forstnerbohrer (mein Set kannst du hier * kaufen)
- Fräser für das Einlassen des Nockenschalters (genutzt habe ich den hier * und den hier *)
- Staubsaugerbeutel (z. B. hier * kaufen)
- Winkel zum Befestigen der Schalterfront (z. B. hier * kaufen)
- Holzschrauben 12 mm habe ich genommen für die Befestigung der beiden Lüftergitter und des Reihenklemmengehäuses (z. B. hier * kaufen)
- Holzleim (musste mir da auch erst neuen holen, den du hier * kaufen kannst)
- Sekundenkleber zum Befestigen der Gewindestangestücke (ca. 5 cm jeweils) in dem Drehgriff (z. B. hier * kaufen)
- Holzbeize (wer auf das Let's-bastel-Rot steht, nimmt die hier *, ich habe meine von Hornbach in dunkelrot)
- Werkzeug zum Verbinden der Elektrik
Ich habe mich letztlich für die Eltako-Anschaltautomatik entschieden, da es die wohl immer geben wird, im Gegensatz zur Anschaltautomatik von Let's bastel. Außerdem habe ich dort Gewährleistung drauf, bei der Let's-bastel-Anschaltautomatik hätte ich außerdem selbst löten müssen, was ich nicht möchte. Aber das kann ja jeder machen, wie er oder sie will.
Elsa, die Zerstörerin
Ja, an irgendeinem Nachmittag im Juni 2020 war es so weit und ich habe meinen ersten Staubsauger auseinander genommen. Was sich immer so einfach angehört hat, ist in Wirklichkeit Schweißarbeit ;-) Letztlich war es aber eine Erfahrung wert und die Belohnung ist eine Turbine, die man im Notfall nochmal austauschen kann, wenn sie kaputt gehen sollte.
Ohne Michael wäre ich nie auf so eine Idee gekommen, daher bin ich ganz froh, dass er dazu Videos gemacht hat und die Pläne bereitstellt.
Der Zusammenbau
Das Holz - 18 mm dickes Multiplex - hatte ich mir bei Hornbach schon zusägen lassen, da ich keinen Anhänger habe, keine Anhängerkupplung und wegen den paar Teilen keine Lieferung machen wollte. Klar, es ist auf den ersten Blick teurer, aber ich hätte es von dort ja gar nicht wegbekommen.
Bei Hornbach ist es so, dass es zwei unterschiedliche Methoden gibt. Entweder ihr nehmt die ganze Platte und lasst sie euch im Markt zuschneiden oder ihr nehmt das Online-Zuschnittstool.
Bei der ersten Variante bezahlt ihr die Platte und nehmt die Teile, die übrig bleiben, mit. Der erste Schnitt ist zwar kostenlos, für jeden weiteren wird aber ein Euro je Schnitt (!!) fällig. Da man ja die Leute nicht aufhalten will, ist es bei dieser Variante so, dass ihr besser schon alle Teile und Maße dabei habt, wenn ihr zum Zuschnitt geht. Nicht dass ihr erst im Laden überlegt, welche Teile und Maße ihr braucht ;-)
Bei der zweiten Variante habt ihr überhaupt keinen Verschnitt, ihr nehmt auch nicht die Plattenreste mit, bezahlt dafür aber einen höheren Preis je m². Außerdem könnt ihr das online alles schon reservieren und könnt dann nochmal selbst prüfen, ob alles stimmt.
Beim Zusammenbauen musst du immer darauf achten, überall schön viel Holzleim rein zu schmieren, das gibt nochmal ein bisschen Dichtigkeit, wenn er trocknet. Ich hatte es so gemacht, dass ich erst alles ohne Leim zusammengebaut hatte und dann alles noch einmal auseinandergeschraubt habe, um es dann mit Leim richtig fest zu verbinden. Das hat aber nur den Hintergrund, dass ich meine Projekte gleich komplett sehen möchte, ehe ich es für die Ewigkeit zusammenbringe. Allerdings kann ich nur davon abraten, das so zu machen, denn bei mir ist es an dieser Stelle irgendwie zu Schwankungen gekommen, als plötzlich eine Seite des ganzen Innengehäuses 5 mm versetzt war. Das bedeutete im Umkehrschluss, die Fräse anzuschmeißen und es geradezubiegen, indem man bisschen was wegfräst.
Den Nockenschalter einlassen war etwas, was extrem viel Zeit in Anspruch nahm. Das hatte aber nur den Grund, dass ich erst nicht genau wusste, wie ich es nun am besten anstelle, dass es gerade ist und nicht zu weit weggefräst. Ich habe also mit der Bandsäge das Quadrat von 50 x 50 mm freigelegt und dann mit der Makita-Oberfräse RT0700CX2J (hier * kaufen) das Quadrat im richtigen Holz abzuarbeiten. Ich habe ja zwei Fräser mit Kugellager oben, die ich auch beide gebraucht habe, aber das war nicht das Gelbe vom Ei. Dabei habe ich mich verfräst und das Ausschneiden des Quadrats mit meiner nicht gut funktionierenden Bandsäge hat dafür gesorgt, dass das gar nicht gerade war. Das siehst du auf den Bildern unten auch, aber letztlich ist es ja nur innen, was niemand mehr sehen wird ;-)
Als Holz für die "Drehknaufe" an den unteren drei Fronten habe ich Zirbenholz genommen, welches mir eine Bekannte gegeben hatte. Da brauchte ich nicht viel weg schneiden. Dort kommt ein 5-mm-Bohrer und ein 6-mm-Gewindeschneider zum Einsatz. Befestigt werden die 5 cm langen und 6 mm dicken Gewindestangenstücken, die ich mit dem Winkelschleifer zurecht geflext habe, dann mit einem Tropfen Sekundenkleber in den Holzstücken. Die Holzstücke sind bei mir ca. 20 mm breit, 30 mm hoch und 18 mm stark. Hierbei aufpassen, dass ihr nicht zu tief bohrt oder gewindeschneidet, das ist mir einmal auch passiert.
Was würdest du anders machen bzw. was hast du gelernt?
Das Wichtigste ist, dass ich nie wieder einmal zusammenbauen würde, um es dann wieder auseinanderzubauen und mit Leim nochmal zusammenzubauen. Hierbei ist mir auch ein Schraubenkopf abgebrochen, was mir vorher noch nie passiert ist.
Auch würde ich für das Einlassen des Nockenschalters eine Frässchablone entweder selbst bauen oder kaufen. Die Variante, die ich genommen habe, ist mehr als ungünstig. Weil ich aber sehr Zeitdruck hatte, musste die oben beschriebene "schnelle" Lösung her.
Zu den Karosseriescheiben ist leider überhaupt nichts in den Videos gesagt worden und auch in den Plänen findet man nichts dazu. Das Abschleifen ist sehr, sehr aufwendig, aber für mich noch die beste Variante gewesen.
Die "Fräsungen" an den ersten drei Fronten von unten für die Befestigung der Karosseriescheiben mit den Außenseiten würde ich nicht mehr mit dem Dremel machen, sondern mir einen neuen kaufen. Hier wäre es hilfreich gewesen, wenn in den Plänen gleich ein Maß benannt worden wäre, was man sich direkt am Anfang mit anzeichnen kann und gleich bearbeiten kann.
Das Thema Holzbeize war für mich eine komplett neue Erfahrung. Das Beizen an sich war nicht das Problem, aber die "Endbearbeitung" war eins. Ich hatte die gebeizten Teile mit Arbeitsplattenöl überstrichen, aber nun habe ich das Problem, dass alles abfärbt. Ich könnte mir vorstellen, dass ich das irgendwann nochmal mit Lack bearbeiten werde, da ich keine Lust auf rote Finger habe, denn ich habe mich wirklich nicht verletzt ;-)
Zu der Eltako-Anschaltautomatik ist nur eins zu sagen: sie tut, was sie tun soll, allerdings könnte die Nachlaufzeit besser geregelt sein. Ich habe sie auf der kleinsten Stufe, was aber tatsächlich zu kurz ist. Die nächst längere Nachlaufzeit wäre aber schon wieder zu lang, ich glaube, es ist eine halbe Minute. Etwas dazwischen wäre echt nicht schlecht.
Alles in allem war es eine gute Erfahrung, die bei mir für viel Muskelkater gesorgt hat.
Dass es die Pläne schon gab, war einerseits gut, weil ich es dann nicht erst selbst zeichnen musste (und ich sowieso noch keine Ahnung von dem Prinzip hatte, bevor ich angefangen habe), andererseits verlässt man sich dadurch natürlich extrem auf die Pläne. Allerdings habe ich aber auch nicht so ganz 100 % nach den Videos gearbeitet, da ich in der Werkstatt keine Lust auf so viele Videos hatte. Nur wenn ich mal nicht weiter wusste, musste ich dann erst das richtige Video mit der richtigen Stelle suchen. Hier wäre es echt praktisch gewesen, man hätte alles in die Baupläne gepackt, damit man nicht erst suchen muss.
Wenn du Fragen an mich hast, schreibe mir gerne über das Kontaktformular.