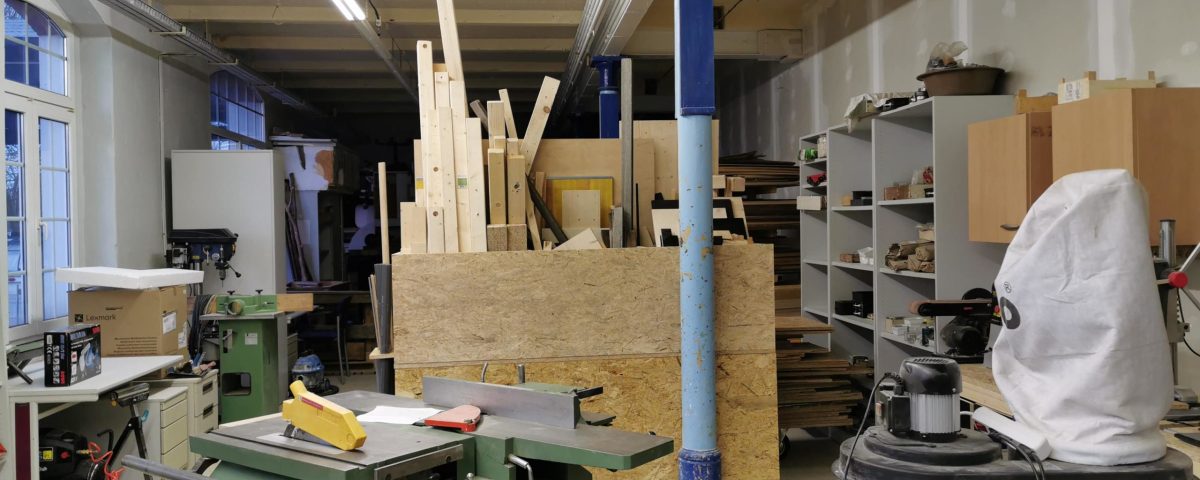
Als ich in die neue Werkstatt gezogen bin, haben wir ein Holzlager für die OSB-Platten, Kanthölzer, Bohlen und sonstige Holzstücke gebaut. Das war so riesig groß und so schwer, dass ich es nicht mehr alleine bewegen konnte. Darunter waren noch die Möbelroller vom Umzug.
Der Anfang vom Ende
Irgendwann kamen die großen Rollen (hier kaufen *, ich habe aber die mit 200 mm Durchmesser, die es derzeit nicht mehr gibt) und ich wollte sie an das schon bestehende Holzlager anbringen.
Es musste erst das ganze Holz (inkl. OSB-Platten *uff*) vom Wagen heruntergeholt werden. Schon das alleine dauerte einige Stunden. Als wir fertig waren, habe ich die Rollen angefangen darunter zu schrauben, was mehr schlecht als recht funktionierte.
Das Hauptproblem war, dass ich zu tief gebohrt hatte und die Schlossschrauben sich nicht mehr ins Holz "bohrten". Da auch noch die Schrauben ein paar winzige mm zu lang waren, musste ich Leisten darauf schrauben. Als dann alles fertig waren, haben wir einige Stunden wieder das ganze Holz darauf gelegt, bis ............ ja, bis es *knack* machte und sich die OSB-Platten ganz unten von den Metallstangen lösten :-( Aber schon da merkte ich, dass der ganze Wagen trotz der supergroßen Rollen sich nicht mehr bewegte, weil es einfach alles zu schwer war.
Neuer Plan musste her
Da ich mich an diesem Tag schon wieder so aufgeregt hatte - so viele Stunden umsonst gearbeitet - habe ich am gleichen Abend angefangen, ein neues Holzlager zu planen. Einige Videos bei YouTube dazu angeschaut und mich dann für etwas entschieden, bei dem gleich meine HT-Rohre Platz finden können. In den HT-Rohren sollen Rundstäbe oder Metallstäbe rein, damit die auch gleich aufgeräumt sind. Das Ergebnis kannst du in den Bildern unten sehen.
Holzlager Nr. 2
Nachdem der Plan stand, wusste ich, dass ich das Lager einmal unverleimt zusammenbauen möchte und danach verleime.
Also kam irgendwann der Tag, an dem ich einige der OSB-Platten zersägt habe. Da das Lager 1,80 m lang werden sollte, hieß es, mit der Tauchsäge und der Führungsschiene zu sägen. Leider war auch das nicht ganz 100 % gerade, aber für das Lager reichte es allemal ;-)
Nachdem die Teile zugesägt waren, kam die erste größere bzw. langwierige Herausforderung... die Flachdübel fräsen. Da ich doch etwas sehr ungeduldig bin, wenn es um so etwas geht, war es mitten im Projekt plötzlich eine Horrorvorstellung, vielleicht 100 Flachdübel zu nutzen und das Ganze auch noch zuvor zu fräsen.
Was war schwierig?
Zuerst: So viel Geduld zu haben. Aber auch der Verleimprozess an sich wäre alleine überhaupt nicht möglich gewesen. Zum Glück hatte ich zwei helfende Hände, sodass es dann doch recht schnell ging und relativ gut.
Was sich während des Baus auch noch als etwas knifflig herausstellte, war die Stelle, in die die HT-Rohre kommen sollten. Hier musste ich den Kreisschneider mit dem Akkuschrauber nutzen. Keine Angst, ich habe ihn mit zwei Händen gehalten. Das kann aber auch schnell nach hinten losgehen, wenn man nur eine Hand nutzt und die Kraft des Kreisschneiders nicht einschätzen kann!
Was würdest du anders machen?
Auf alle Fälle würde ich vorher die HT-Rohre messen ;-) Da ich dachte, die wären alle 1 m lang, habe ich die Halterung für die Rohre mit ca. 70 cm Abstand zum oberen Ende geplant und dann gleich verleimt.
Hätte ich vorher gemessen, hätte ich gemerkt, dass das große HT-Rohr mit 11 cm nur rund 60 cm ist. Also fehlten da einige cm nach oben hin. Erst einmal lasse ich es so, aber irgendwann wird das geändert.